MIG 250: Unleashing the Power of Efficient Welding for Electricity Suppliers
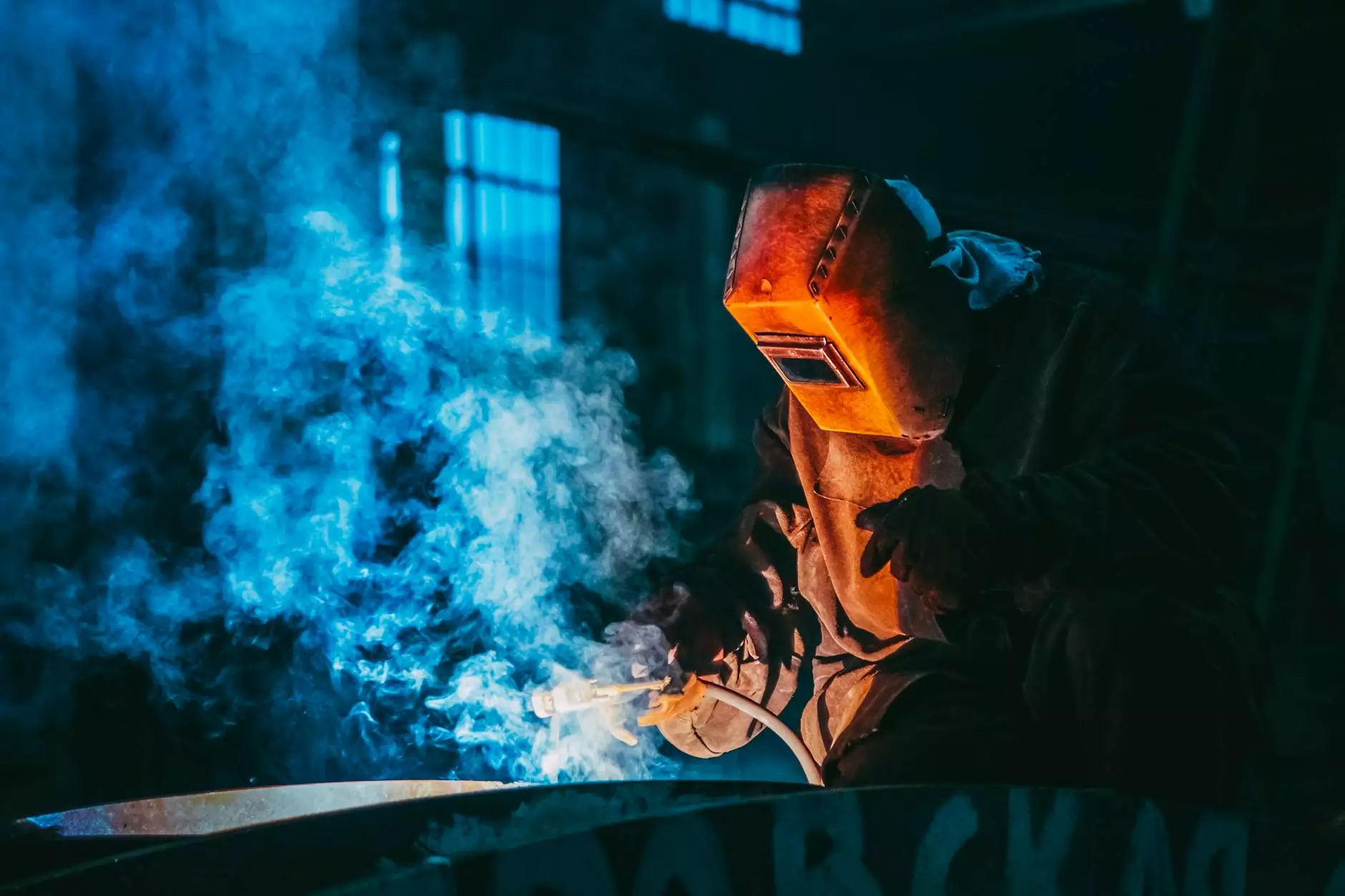
The electrification of industries is a transformative force in the global economy, and with it comes the need for reliable and efficient systems. Among the crucial components supporting this progression is welding technology. In particular, the MIG 250 welding system stands out as an exceptional tool in the arsenal of electricity suppliers. This article delves deep into the advantages, applications, and operational efficiencies provided by MIG 250 welding technology.
Understanding MIG Welding Technology
MIG, or Metal Inert Gas welding, is a process that uses a continuous wire feed as an electrode and an inert gas to protect the weld from contamination. This process is favored for its ability to create high-quality welds efficiently and with minimal cleanup. The MIG 250 system specifically refers to machines that operate at 250 amps, providing a robust solution for heavier materials and thicker sections.
The Components of MIG 250 Welding
- Welding Machine: The heart of any MIG welding setup is the machine itself. The MIG 250 features a powerful and adjustable output, allowing for a variety of welding applications.
- Welding Wire: A consumable electrode composed of a metal that melts during the welding process.
- Inert Gas: Typically argon or a mix of argon and CO2, this protects the weld from atmospheric contamination.
- Welding Torch: A tool that directs the wire feed and gas towards the workpiece.
- Workpiece: The material being welded, which is often made of steel, aluminum, or other metals.
Advantages of Using MIG 250 in Electricity Supply Businesses
The MIG 250 welding system offers a plethora of advantages, enhancing operations within the electricity supply sector. Here are some of the key benefits:
1. Enhanced Efficiency
MIG welding, particularly with the MIG 250, allows for faster welding speeds. This efficiency is paramount in the electricity supply sector, where time is money. The automatic feed of the welding wire means that operators can maintain a continuous progress, reducing downtime.
2. High-Quality Welds
The MIG 250 produces clean and strong welds that require less finishing work. This is crucial in maintaining the integrity and longevity of electrical systems. The consistent flow of the wire and the shielding gas ensures that the welds are uniform and free from defects.
3. Versatile Applications
This system is suitable for welding various materials and thicknesses, making it adaptable for different projects within electricity supply. Whether you are working on infrastructure, girders, or electrical cabinets, the MIG 250 has you covered.
4. Reduced Preparation Time
Unlike other welding methods, MIG welding with the MIG 250 requires minimal preparation. It can take on rusty or dirty surfaces effectively, which means less time spent on cleaning the metal and more time for actual welding.
5. Cost-Effectiveness
Investing in a MIG 250 system can lead to long-term savings for electricity suppliers. With reduced labor costs due to faster weld times and lower energy consumption compared to traditional welding systems, the overall operational costs can be significantly minimized.
Applications of MIG 250 Welding in the Electricity Supply Industry
The applications of MIG 250 within electricity supply are extensive and varied. Here are some prominent areas where this technology shines:
1. Electrical Panel Fabrication
MIG 250 is ideal for creating electrical panels, with its capability to handle various thicknesses of metal. The precision of the MIG process ensures that panels fit together seamlessly, enhancing both safety and functionality.
2. Transformer Casing
Welding transformer casings demand strong, rigid constructions that can withstand vibrations and thermal expansions. The MIG 250 provides the strength needed for such applications, ensuring long-lasting durability.
3. Support Structures
Electrical supply systems often require robust support frameworks. The strength of welds produced by the MIG 250 guarantees that these frameworks can endure significant loads and stresses.
4. Distribution Boards
Distribution boards are critical in managing electricity supply. The MIG welding system excels at producing precise, high-quality joints that improve the safety and functionality of these boards.
5. Conduit and Fittings
MIG 250 allows for clean joints in conduits and fittings, making it easier to assemble complex electrical installations. This not only speeds up the installation process but also enhances the overall structural integrity.
Safety and Operational Considerations
Using the MIG 250 welding system does come with certain safety considerations. Here are some crucial aspects to keep in mind:
1. Personal Protective Equipment (PPE)
Welders should always use appropriate PPE, including gloves, helmets with appropriate shielding, and clothing that covers the skin to avoid burns. The intensity of MIG welding creates bright arcs that can cause eye damage if not taken seriously.
2. Ventilation
Welding emits fumes that can be harmful when inhaled. Ensure that the welding area is well-ventilated or has proper fume extraction systems in place to maintain a safe environment.
3. Electrical Safety
As with any electrical equipment, it is vital to follow strict electrical safety guidelines while operating the MIG 250. Proper grounding and circuit protection devices should always be used to prevent electrical hazards.
Maintenance and Care of MIG 250 Welding Systems
To ensure that your MIG 250 welding system performs optimally, regular maintenance is essential. Here are some maintenance tips:
1. Regular Cleaning
Clean the welding machine regularly to prevent dust and grime build-up that could affect performance. Pay special attention to the contact tip and nozzle.
2. Check Gas Levels
Monitor your gas levels frequently. Low gas levels can lead to poor weld quality and are a common source of frustration for welders.
3. Inspect Cables and Connectors
Frequent inspection of cables and connectors can help identify potential wear and damage before they become serious issues. Always replace frayed or damaged cables to ensure safety.
4. Calibration and Settings
Ensure that the settings on your MIG 250 are calibrated for the particular metal and thickness you are working with. Wrong settings can lead to poor weld quality.
The Future of MIG Welding in Electricity Supply
The advancing technology in the field of welding is continually improving. The MIG 250 system stands at the forefront of these developments, evolving to meet the complex demands of modern industries. With the integration of automation and artificial intelligence, the future holds the promise of even greater efficiencies.
As the electricity supply sector grows and innovates, adopting advanced welding systems like MIG 250 will be crucial for maintaining competitive advantages. The ability to produce strong, reliable connections quickly and effectively will continue to be a major factor in the success of electricity suppliers.
Conclusion
In conclusion, the MIG 250 welding system is an indispensable asset for electricity suppliers. Its efficiency, versatility, and reliability make it the preferred choice for a wide variety of welding tasks. Embracing the strengths of MIG technology not only enhances operational capabilities but also ensures that the quality of service provided is second to none. As industries evolve, so too should their methods — and MIG welding technology will undoubtedly lead the charge towards a more efficient and effective future in electrical supply.